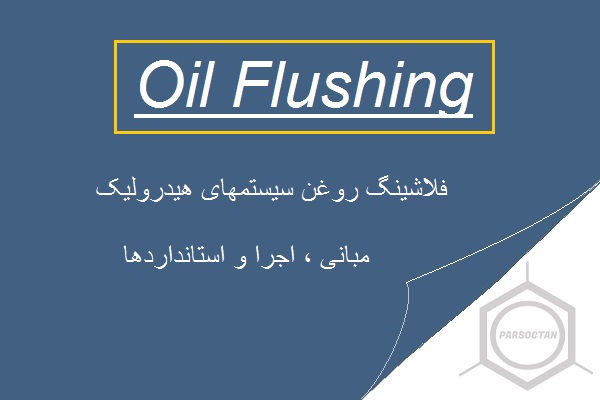
آشنایی با فلاشینگ روغن سیستم های هیدرولیکی در صنایع – فلاشینگ روغن لوله و تجهیزات ، استانداردهای فلاشینگ و ذرات مجاز روغن
فلاشینگ روغن چیست و چرا فلاشینگ می کنیم ؟
مقدمه: سیستمهای هیدرولیک و تجهیزاتی که در مسیر سیستم های هیدرولیکی قرار دارند نسبت به تمیزی و خلوص سیال هیدرولیک بسیار حساس هستند بطوریکه بیش از 70 درصد خرابی این تجهیزات ، طبق آمار، به علت آلودگی روغن و سیال هیدرولیک است.
لذا در سیستمهاي هیدرولیک پایین نگه داشتن سطح آلودگی روغن و تمیز کارکردن یک اصل مهم به شمار می رود.
با اینکه در این سیستمها همواره از فیلتر استفاده میگردد، ولی گاهی به علتهای مختلف که مهمترین آنها تعمیرات جزیی و باز بست کردن قسمتهای سیستم است، آلودگی وارد سیستم هیدرولیک شده و باید این آلودگی برطرف گردد که در این مواقع سیستم را اصطلاحا فلاشینگ می کنند.
برای فلاشینگ به طور خلاصه، کل سیستم از ابتدا تا انتها را در یک مدار بسته شامل پمپ و تانک روغن و فیلترهای مورد نیاز می بندند و روغنی مشابه با روغن اصلی سیستم را برای ساعتها در مسیر می چرخانند تا کل ذرات و آلودگی ها با روغن فلاشینگ حمل شود و در فیلترها به دام افتد.
البته باید توجه داشت که این آلودگی ها شامل انواع مختلفی هستند مانند : آلودگی ذرات، آلودگی آب، آلودگی مخلوط شدن با روغن دیگر ، آلودگی خرابی روغن در اثر افزایش حرارت، آلودگی هوا.
ولی از انجایی که مهمترین آنها آلودگی ذرات معلق است، در این مقاله تمرکز بیشتری بر این نوع آلودگی خواهیم داشت و در این مقاله اصول فلاشینگ ، روش صحیح فلاشینگ و استانداردهای فلاشینگ روغن هیدرولیک را بررسی خواهیم کرد.
روش اجرای عملیات فلاشینگ روغن در سیستم هیدرولیک :
تئوری فلاشینگ روغن :
فلاشینگ عبارتست از جدا سازی ذرات آلوده از روغن و سیستم هیدرولیک به کمک فیلتر با سرعت جریان سیال بالا و دماي مناسب. در این شرایط روغن با سرعت بالا و به کمک جریان مغشوش، ذرات موجود در سیستم و جداره هاي داخلی لوله ها و منافذ را جدا کرده و پس از عبور دادن آنها از کلیه مسیرها در آخر توسط فیلتر ها جدا می شوند.
برای دستیابی به حداکثر کارایی در این عملیات ، ما نیاز داریم که 3 پارامتر کلیدی را کنترل کنیم که عبارتند از : 1. جریان مغشوش 2. ویسکوزیته سیال 3. زمان فلاشینگ
اغتشاش در جریان سیال برای غوطه وری ذرات آلوده کننده برای سیستم هیدرولیک بسیار مهم است که ما برای این منظور نیاز داریم همواره عدد رینولدز را بر روی عدد 4000 نگاه داریم. لذا استفاده از پمپ با دبی مناسب بسیار مهم خواهد بود.
ویسکوزیته مناسب برای فلاشینگ ، 10 تا 15 سانتی استوک در دمای 40 درجه است .برای کنترل ویسکوزیته و گرانروی سیال نیز باید دمای روغن فلاشینگ را به محدوده 40 تا 60 درجه سانتی گراد برسانیم.
زمان مورد نیاز براي این امر بسته به میزان آلودگی سیستم داشته و حداقل زمان موردنیاز طبق فرمول زیر قابل محاسبه خواهد بود: T=V/Q*3
این زمان حداقل مورد نیاز می باشد. (نکته مهم اینست که باید توجه داشت این فرمول تنها حداقل زمان است و در حین فرآیند فلاشینگ باید فیلترها از لحاظ آلودگی بازرسی شوند. پس از این حداقل زمان، با نمونه گیری از روغن و سنجش آلودگی در آزمایشگاه ادامه فرایند فلاشینگ مشخص خواهد شد و هیچگاه زمان مشخصی برای فرایند نمی توان تعیین کرد.)
اجرای عملیات فلاشینگ :
از نظر اجرای عملیات ، فلاشینگ روغن به دو نوع فلاشینگ داخلی (Internal) و فلاشینگ خارجی (External) تقسیم بندی می شود.
تفاوت فلاشینگ داخلی و خارجی چیست ؟
اگر سیستم آلودگی کمی داشته باشد ، تنها شیرها و قطعات حساس به آلودگی باز می شوند و به کمک یونیت و پمپهای اصلی خود سیستم ، عملیات فلاشینگ انجام می شود که به آن فلاشینگ داخلی می گویند.
در این روش نیازی به یونیت و فیلترهای مجزا نداریم. ابتدا کلیه قطعات حساس از سیستم باز شده و بجای آنها ولو بای پاس و یا Plate راه دهنده بسته می شود. و سپس مسیر چرخشی از مخزن و پمپ به لوله ها و مجددا مخزن ایجاد می شود. همچنین فیلتر هاي خود سیستم وظیفه تمیز کردن روغن آلوده شده فلاشینگ را برعهده دارند.
ولی اگر سیستم تا بحال مورد بهره برداری نبوده و تازه تجهیزات نصب شده باشد ، و یا عملیات تعمیرات وسیعی انجام شده که موجب آلودگی شدید در سیستم شده باشد ، در این حالت ما به یک یونیت جداگانه نیاز داریم . چرا که مش بندی فیلترها باید از درشت به ریز تغییر کند تا هزینه گزافی برای فیلترها متحمل نشویم. همچنین پمپهایی با فشار بالاتر استفاده شود تا عدد رینولدز بالاتر و اغتشاش بیشتر ایجاد کنیم.
اصول کار فلاشینگ داخلی تماما مشابه فلاشینگ خارجی خواهد بود .در اینجا ما با توجه به اهمیت فلاشینگ خارجی و نکات مهمی که این عملیات دارد ، بیشتر بر این نوع از فلاشینگ سیستم هیدرولیک تکیه می کنیم و مراحل کار را طبق تیترهای زیر شرح خواهیم داد:
- آماده سازی سیستم
- آماده سازی یونیت فلاشینگ
- اتصالات و لوپ بندی
- اجرای عملیات
- نمونه گیری و آنالیز روغن
آماده سازی سیستم :
در اینجا منظور ما از سیستم ، یک واحد صنعتی هیدرولیک است که شامل تجهیزات هیدرولیک ، لوله ها ، ابزاردقیق و شیرآلاتی است که بر روی لوله ها بسته شده است.
آماده سازی سیستم شامل کارهایی است که باید قبل از اتصال به یونیت فلاشینگ انجام دهیم . یک بخش از این آماده سازی ، باز کردن تمامی تجهیزات ابزار دقیق و ولوهای حساس به آلودگی در مسیر است.
بخش دیگر ، تمیز کاری اولیه سیستم است که بیشتر شامل لوله میشود. ممکن است داخل لوله مواد خارجی مانند لاستیک، پارچه ، گرد و غبار باشد که می توان با استفاده از هواي فشرده آنها را خارج نمود. پس از آن باید تا جایی که امکان دارد ، ذرات آلوده کننده را از لوله ها پاک کنیم که متحمل هزینه و کار کمتری هنگام فلاشینگ شویم.
به این منظور ، اگر جنس لوله های سیستم از استنلس استیل باشد (که اغلب در سیستمهای هیدرولیک چنین است) میتوانیم به هوای فشرده برای خارج سازی آلودگی بسنده کنیم و یکبار جهت اطمینان با مقداری روغن لوله را فلاش کنیم و روغن را دور بریزیم و سپس فلاشینگ اصلی را شروع کنیم.
ولی اگر جنس لوله ها کربن استیل باشد ، ممکن است لوله ها حاوی آلودگی بسیاری شامل چربی و زنگار و براده آهن باشند که کار کمی سخت تر میشود.
برای تمیزکاری و آماده سازی لوله کربن استیل جهت فلاشینگ ، باید لوله ها را شستشوی شیمیایی کنیم. در مطالب پیشین مراحل کامل شستشوی شیمیایی لوله کربن استیل (به طور کلی و برای مقاصد مختلف) توضیح داده شده که میتوانید به آن مراجعه کنید. در اینجا توضیح مختصری خدمت شما ارائه میکنیم:
شستشوی شیمیایی شامل 4 مرحله میباشد: 1 ) چربی زدایی : در این مرحله لوله را با حلال چربی زدا با دماي 70 درجه شستشو میدهند که چربی زدا معمولا ترکیبی از قلیاهای قوی و ضعیف انتخاب می شود مانند سود سوز آور (NAOH) به همراه کربنات کلسیم ، بیکربنات کلسیم و مانند آن.
2) اسید شویی : پس از چربی زدایی یکبار فلاشینگ آب داریم و پس از آن لوله را با محلول 10 تا 15 درصد اسید شستشو می دهند تا زنگار از سطح آن کنده شود. محلول اسید شامل HCL (برای زنگار زیاد) و یا اسید سیتریک (برای لوله های نسبتا تمیز) است.
3) خنثی سازی : در مرحله سوم باید اسید خنثی سازی شود که معمولا برای اینکار از محلول آبی آمونیاک استفاده میشود.
4) و اما مرحله چهارم که پسیویشن (Passivation) نام دارد. اگر این مرحله به درستی انجام نشود تمامی زحمات ما برای شستشوی شیمیایی بیهوده بوده است.
هدف از این مرحله ایجاد فیلمی نازک بر روی سطح آهن است که باعث میشود نسبت به خوردگی مقاوم (یا اصطلاحا PASSIVE ) شود. محلول مورد نیاز هم معمولا نیتریت سدیم می باشد.
نکته بسیار مهم اینست که جدأ باید از اسید شویی منیفولد و تجهیزات هیدرولیکی اجتناب کرد.
همچنین پس از انجام عملیات باید محلولهای شستشو کاملا تا قطره آخر از لوله خارج و با هوای فشرده Blow-out و خشک کردن انجام شود و تا زمان شروع فلاشینگ روغن ، لوله ها بسته و اصطلاحاُ CAP شود. (به جهت اظمینان، باید یکبار با مقداری روغن مخصوص فلاشینگ، لوله ها فلاش شوند و این روغن دور ریخته شود)
آماده سازی یونیت فلاشینگ روغن :
یونیت فلاشینگی که در کارگاه های مختلف استفاده میشود عمدتأ توسط شرکتهایی که متخصص انجام فلاشینگ هستند بصورت آماده کرایه میشود چرا که از نظر اقتصادی ساخت یک یونیت مجهز برای پروژه فلاشینگ مقرون به صرفه نیست. مگر در مواردی خاص، به عنوان مثال کارخانجات فولاد را میتوان نام برد . در صنعت فولاد واحدهای هیدرولیکی که وجود دارند باید دوره ای فلاشینگ شوند لذا در فولاد معمولأ یک یونیت فلاشینگ در انبار میتوان پیدا کرد.
در اینجا به بررسی این موضوع می پردازیم که یونیت فلاشینگ چیست و برای کار مورد نظر ما چه خصوصیاتی باید داشته باشد:
یونیت فلاشینگ به یک یونیت پرتابل و مجهز اطلاق می گردد که شامل پمپها ، مخزن برای جمع آوری روغن و کارتریج فیلتر است. شکل شماتیک و واقعی یک یونیت فلاشینگ را میتوانید در تصاویر زیر مشاهده نمایید:
پمپ یونیت باید از یک موتور قوی با دبی مورد نیاز (بستگی به سیستمی که میخواهیم فلاشینگ کنیم) بهره مند باشد که بتواند عدد رینولدز 4000 که برای عملیات نیاز داریم را تامین کند.
مخزن فلاشینگ محل جمع آوری روغن و تغذیه پمپ به درون خطوط سیستم است. از خصوصیات مهم این مخزن اینست که باید ترجیحأ گالوانیزه باشد ، مجهز به هیتر های قابل کنترل باشد (برای افزایش دمای روغن تا 70 درجه) و شیر نمونه گیری بر روی آن نصب شده باشد.
کارتریج فیلترهای یونیت باید در سایز مناسب فیلترهایی که میخواهیم استفاده کنیم باشد و عاری از هرگونه آلودگی و قابل آب بند کردن باشد.
لوپ بندی و اتصالات :
لوپ بندی به عملیاتی اطلاق میگردد که طی آن سیستم و یونیت فلاشینگ در یک مدار سری بسته قرار می گیرند و آماده استارت چرخش روغن می شوند.
لوپ بندی کار بسیار دقیق و حساسی است که باید حتمن با حضور ناظر و اپراتور و فیترهای باتجریه در فلاشینگ انجام گردد. هرگونه کوتاهی و بی دقتی ممکن است خطرات جانی برای پرسنل و هزینه های گزافی برای شرکت ایجاد کند.
برای لوپ بندی باید ابتدا ولوها و تجهیزات ابزاردقیق درآورده شود، به جای آنها کانکشن های موقت (Temporary) نصب گردد ،کلیه عملگرها شامل سیلندرها و هیدروموتورها از مدار خارج گردند. کلیه اتصالات لوله کشی از محل والو استندها و مانیفولدهاي هیدرولیک و همچنین پمپ هاي هیدرولیک باز شوند.
سپس لوله ها طبق نقشه های پلن و آیزومتریک انتخاب شوند ، و انتهای هر لوله به ابتدای لوله بعدی متصل گردد.
مدار باید به شکلی بسته شود که از گردش روغن در همه مدار و عدم ایجاد هوا در مدار اطمینان حاصل شود. در صورت نیاز ، مناطق خاصی شامل ونت (Vent) باشد.
لوپ بندی باید به شکلی باشد که سرعت و دمای در تمامی نقاط و همه لوله ها یکسان باشد. در صورت نیاز از منیفولدهای موقت استفاده کنید.
شروع عملیات چرخش روغن :
برای شروع عملیات ، روغن را داخل تانک یونیت ریخته و پمپ را استارت میکنیم مراحل و نکات زیر جهت فلاشینگ توصیه می شوند:
1. سیال فلاشینگ باید با سیالی که در سیستم هیدرولیک استفاده می شود سازگار باشد.(به این منظور باید به اسپک های سیستم مراجعه و از نوع روغن هیدرولیک سیستم اطمینان حاصل نمود. به عنوان مثال در سیستمی که سیال آن پایه آب-گلیکول است به هیچ عنوان نباید از روغن استری برای فلاشینگ استفاده کرد.)
2. مسیر برگشت به تانک را باید از فیلترهایی با ظرفیت مناسب عبور داد.
3. سرعت سیال در فرآیند فلاشینگ باید به گونه اي باشد که جریان در کلیه مسیرها مغشوش باشد. (عدد رینولد بزرگتر یا مساوی 4000)
4. حین فلاشینگ، ویسکوزیته سیال در حین کار حدود 10 الی 15 سانتی استوك در دماي 40 درجه سانتیگراد باشد.
5. سرد ترین نقطه در فلاشینگ باید حداقل 50 درجه سانتی گراد دما داشته باشد لذا حداقل دماي سیال فلاشینگ باید 60 درجه سانتی گراد باشد. در برخی موارد می توان براي رسیدن به این دما از عایق کردن لوله ها نیز استفاده کرد.
6. شیرهاي پروانه اي، توپی ،سوزنی و … قطعات مهمی هستند که باید بصورت گرم کامل فلاشینگ گردند.
7. مخزن روغن سیستم، محفظه فیلترها (بادي فیلتر) و سیلندرها باید بطور جداگانه فلاشینگ گردند. بادي فیلتر را می توان بصورت دستی و یا با خارج کردن المان فیلتر در مدار چرخشی فلاشینگ قرار داد تا تمیز گردد. سیلندر هاي هیدرولیک باید با حرکت دادن کل کورس آنها و تکرار آن تمیز شوند.
8. ترجیحا اگر بتوان جریان را متناوبا کم و زیاد کرد جریان ضربه اي می تواند بهتر رسوبات و آلودگی هاي مسیر را جدا کرده و تمیز نماید. (ایجاد اغتشاش در سیال)
9 . سیال را باید قبل از شروع عملیات فلاشینگ گرم کرده تا به دماي مناسب حدود 30 درجه سانتی گراد برسد. این عملیات را باید به کمک هیتر درون مخزن استاندارد انجام داد. (هنگام کار دما در اثر اصطکاک بالا میرود و به دمای مطلوب 60 تا 70 درجه میرسیم)
10. هر نیم ساعت دمای قسمتهای مختلف مدار را چک کنید و مطمئن شوید جایی با دمای کمتر از بقیه سیستم وجود نداشته باشد.
11. بصورت مداوم باید گیج فشار روی کارتریج فیلترها را بررسی کرد . با کثیف شدن فیلتر فشار بالا میرود و موقع تعویض فیلتر است . (هنگام چرخش روغن به هیچ وجه کارتریج را باز نکنید)
12. حداقل زمان فلاشینگ بسته به دبی و حجم مخزن فلاشینگ می باشد که حدودا جهت بررسی اولیه 4 ساعت می باشد.
13. فیلترها از سمت سیستم به سمت تانک ، باید از مش درشت به مش ریز به ترتیب قرار گیرند. توصیه ما تعبیه 3 فیلتر 25 میکرون و 10 میکرون و 3 میکرون است. برای سیستم های حساس نیز 2 میکرون هم اضافه گردد. (برای کاهش هزینه ها میتوانید حدود دو ساعت اول را با فیلتر 40 یا 50 میکرون به تنهایی ، فلاش کنید تا ذرات بزرگ کاملن گرفته شود.)
14. پس از 4 ساعت از سیستم نمونه گیري نموده و میزان تمیزي سیال بررسی شده و شرایط سیستم بررسی گردد.
15. هر 4 ساعت یک مرتبه از سیستم نمونه گیري کرده و شرایط سیستم بررسی گردد. زمان پایان دادن به فلاشینگ ، تنها مستلزم تطابق تمیزی نمونه ( که آنالیز شده) با سطح تمیزی مورد نیاز است. باز تاکید میکنیم : زمان قطعی برای پایان دادن به عملیات فلاشینگ وجود ندارد.
16.هنگامیکه نتایج آزمایشگاه مطلوب بود عملیات را متوقف و کلیه سیال فلاشینگ از سیستم خارج گردد.
17. کلیه قطعات ، شیلنگ ها و اتصالات اضافی که براي مدار چرخشی نصب شده بود باز شده و لوله ها به تجهیزات مربوطه مجددا متصل گردند. (باید توسط تیم متخصص و با وسواس زیاد انجام شود که دوباره آلودگی وارد سیستم نشود)
18. روغن جدید در سیستم اصلی شارژ شده و فلاشینگ را با سیستم اصلی شروع می کنیم.
19. مش فیلتر مناسب براي سطوح تمیزي مطلوب مطابق جدول پیشنهاد زیر می باشد.
تست و آنالیز آزمایشگاهی و استاندارد هاي آلودگی روغن هیدرولیک
پس از انجام فلاشینگ در حداقل زمان درنظر گرفته شده ، باید از روغن نمونه برداری شود و برای تست به آزمایشگاه یا افراد متخصص برای آنالیز سپرده شود.
اصول آنالیز بدین شکل است که اندازه و تعداد ذرات آلوده کننده با استانداردهای موجود مقایسه گردد.
ریز ترین سایز ذرات قابل رویت توسط چشم غیر مسلح حدود 40 میکرون است. این در حالی است که بسیاری از ذرات آسیب رسان به سیستم هیدرولیک، معمولا دارای سایز کوچکتر از 40 میکرون هستند. لذا برای آنالیز باید از دستگاه های آزمایشگاهی و میکروسکوپ (برای بررسی ویژوال) استفاده شود.
برای بیان سطح آلودگی روغن از استاندارد هاي مختلفی استفاده می شود که متداول ترین آنها استاندارد ISO 4406 و NAS 1638 می باشد. استاندارد ایزو به لحاظ دقت استاندارد دقیق تری بوده ولی استاندارد NAS به دلیل سادگی بیشتر متداول است.
استاندارد ISO 4406
در این استاندارد سطح آلودگی روغن با سه عدد بصورت A/B/C نشان داده میشود .
A بیان گر تعداد ذرات موجود در هر میلی لیتر با سایز بیشتر از 4 میکرون ، B بیان گر تعداد ذرات موجود در هر میلی لیتر با سایز بزرگتر از 6 میکرون ، و عدد سوم C با سایز بزرگتر از 14 میکرون است.
به این معنی که اگر کارفرما از ما میخواهد سیستم هیدرولیکی با تمیزی 16/14/11 به او تحویل دهیم ، نتایج آزمایشگاه پس از فلاشینگ باید مقدار ذرات 4 میکرون را بین 320 تا 640 ، تعداد ذرات بالای 6 میکرون را 80 تا 160 و تعداد ذرات بزرگتر از 14 میکرون را 10 تا 20 عدد اعلام کرده باشد.
این اعداد را از کجا آوردیم؟ ! به تصویر زیر دقت کنید تا متوجه موضوع شوید.
جدول زیر دو مثال از نحوه بیان سطح آلودگی روغن برای کدهای 24/22/19 و 16/14/11 داده است.
استاندارد ایزو در نگاه اول کمی گیج کننده به نظر می رسد. اگر راهنمایی بیشتری نیاز دارید در کامنت ها بیان کنید تا جایی که در توان باشد ، با کمال میل پاسخگو خواهم بود.
استاندارد NAS به مراتب راحت تر و کاربردی تر است:
استاندارد NAS 1638
NAS 1638 یک استاندارد بسیار قدیمی ولی کاربردی است. ناشر این استاندارد انستیتو هوافضای آمریکا National Aerospace Standard و آخرین ویرایش NAS 1638 متعلق به سال 1964 می باشد! که هنوز هم کاربرد فراوانی دارد .(بیشتر بخوانید > دانلود NAS 1638 )
در این استاندارد سطح آلودگی روغن با اعداد 00 تا 12 نشان داده میشود. البته باید توجه داشت که این اعداد بیانگر رده های با تعداد ذرات مشخص در 100 میلی لیتر روغن است.
به منظور آنالیز با این استاندارد ، نمونه گیری در حین عملیات انجام شده و صد میلی لیتر از روغن را از کاغذ صافی عبور می دهند و تعداد ذرات شمارش شده و با سطح آلودگی 00 تا 12 مقایسه میشود و اندازه ذرات ، با تصاویری که در این استاندارد موجود است مقایسه میگرد.
به تصویر زیر دقت کنید تا مثالی واضح بزنیم :
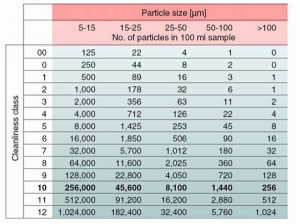
اگر کارفرما سیستمی با تمیزی NAS 10 از ما خواست ، نتایج آزمایشگاهی روغن باید اعلام کند که تعداد ذرات بزرگتر از 100 میکرون 256 عدد ، 50-100 میکرون مساوی 1440 عدد ، 25-50 میکرون مساوی 8100 عدد ، 15-25 میکرون مساوی 45600 عدد و 5-15 میکرون مساوی یا کوچکتر از 256000 عدد است.
نتیجه کلی اینست که آلودگی روغن همواره با دو پارامتر اندازه و تعداد ذرات سنجیده میشود.
خطرات فلاشینگ هیدرولیک و نکات ایمنی فلاشینگ روغن :
در فلاشینگ ما با روغن داغ با سرعت بسیار زیاد در یک سیستم سروکار داریم ، لذا عمده خطرات کاملا مشخص است : خطر پاشیدن روغن داغ به پرسنل ، خطر لیز بودن محیط کارگاهی ، و خطر پاشیدن سیال با فشار بالا.
خطر برخورد سیال با سرعت بسیار بالا از مقاطع باریک به انسان که می تواند باعث سوراخ شدن پوست و نفوذ روغن به داخل پوست گردد. لذا با توجه به اینکه سرعت سیال درون خطوط هیدرولیک در زمان فلاشینگ بسیار بالا می باشد و در صورت استفاده از اتصالات و متعلقات نامناسب می تواند خطر ساز شود لذا لازم است در مدار فلاشینگ حتما از لوله ها، شیلنگ ها، اتصالات و ادوات مناسب استفاده کرده و حتما از محکم بودن اتصالات و باز نبودن هیچ یک از آنها اطمینان حاصل نمود.
با توجه به اینکه دما در فلاشینگ بسیار دارای اهمیت می باشد و بالا بردن دما در این سیستم امري ضروري است لذا خطرات پاشش روغن با سرعت بالا و با درجه حرارت بالا می تواند خطر ساز باشد.
اگر مخزن هیدرولیک بصورت کنترل شده گرم نگردد می تواند باعث رسیدن دماي روغن به میزان دماي اشتعال و یا حتی احتراق روغن گردد و باعث آتش سوزي گردد.
همچنین در صورت کنترل نشدن دما و فشار و اتصالات غیر استاندارد، عملیات میتواند به یک فاجعه ایمنی ختم گردد. لذا جدی گرفتن ایمنی در فلاشینگ روغن باید به اپراتورها و بازرسین همواره گوشزد گردد.
ملاحظات ایمنی فلاشینگ :
از آنجایی که دما و سرعت و فشار سیستم باید کنترل شده باشد ، در زمان اجرای فلاشینگ، حضور یک بازرس حرفه ای حتما لازم است . این بازرس باید به سیستم هیدرولیک و فلاشینگ روغن مسلط باشد و كنترل هاي لازم را انجام دهد و موارد غیر عادي را تشخیص دهد.
استفاده از لوازم حفاظت فردي بر سیستمهای هیدرولیک و فلاشینگ لازم و ضروري بوده و در صورت عدم استفاده میتواند منجر به آسیب به فرد و حتی مرگ گردد. لوازم ایمنی ضروری حین فلاشینگ عبارتند از: کلاه ایمنی، دستکش ضد روغن، عینک محافظ ،کفش ایمنی، لباس ایمنی .
در زمان فلاشینگ لازم می شود از وضعیت آلودگی سیستم در فلاشینگ اطلاع کسب کرد که لازم است از سیستم نمونه گیری گردد لذا حتما در زمان نمونه گیری از تجهیزات نمونه گیری مناسب جهت نمونه گیری از خطوط مختلف به خصوص نمونه گیری از خطوط فشار بالا استفاده گردد.
هنگام بازرسی از سیستمهاي هیدرولیک از نور کافی در محیط بهره ببرید و از تست محل هاي نشتی با دست بپرهیزید چرا که میتواند روغن خروجی بصورت سیال نازك به دست شما وارد شده و آسیب برساند و یا به دلیل لغزنده بودن سطح در محل سیستمهای هیدرولیک باعث سر خوردن و سقوط گردد.
حتما از یونیت فلاشینگ استاندارد شرکت هاي معتبر و با مشاوره از کارشناسان خبره آنها استفاده کنید.
قبل از انجام فلاشینگ دستورالعمل مربوط به فلاشینگ را بررسی و مطالعه نموده و مطابق با آن اقدام نمایید.
از سازنده و طراح تجیهزات دستورالعمل فلاشینگ را بخواهید و یا این عملیات را به آنها واگذار نمایید.
منابع :
1. Ito, T. (1984). Hydraulic System Flushing. FRH Journal.
2. Arnold Krielen and Hans H. Faatz, The production and Installation of Pipework, Bosch Rexroth Corporation.
3. Gibbons, Tom. (1998). Improved Flushing Techniques for Turbine Lube Systems. Pall Corporation Presentation.
4. ISO 5910 Hydraulic Fluid Power. Cleaning of Hydraulic Pipe Systems.
5. ISO 5911 Hydraulic Fluid Power. Methods for Coding Levels of Contamination by Solid Particles.
6.ایمنی در فلاشینگ روغن ، بیژن دیبایی نیا و مسعود هراتیان
———————————————
پایان
نویسنده : رامین مرادی / وبسایت پارس اکتان
با نظرات سازنده خود، به بهتر شدن این مقاله کمک نمایید. در صورت نیاز به مشاوره و راهنمایی خصوصی در رابطه با پروژه های فلاشینگ نیز میتوانید از طریق راههای ارتباطی با ما در تماس باشید.